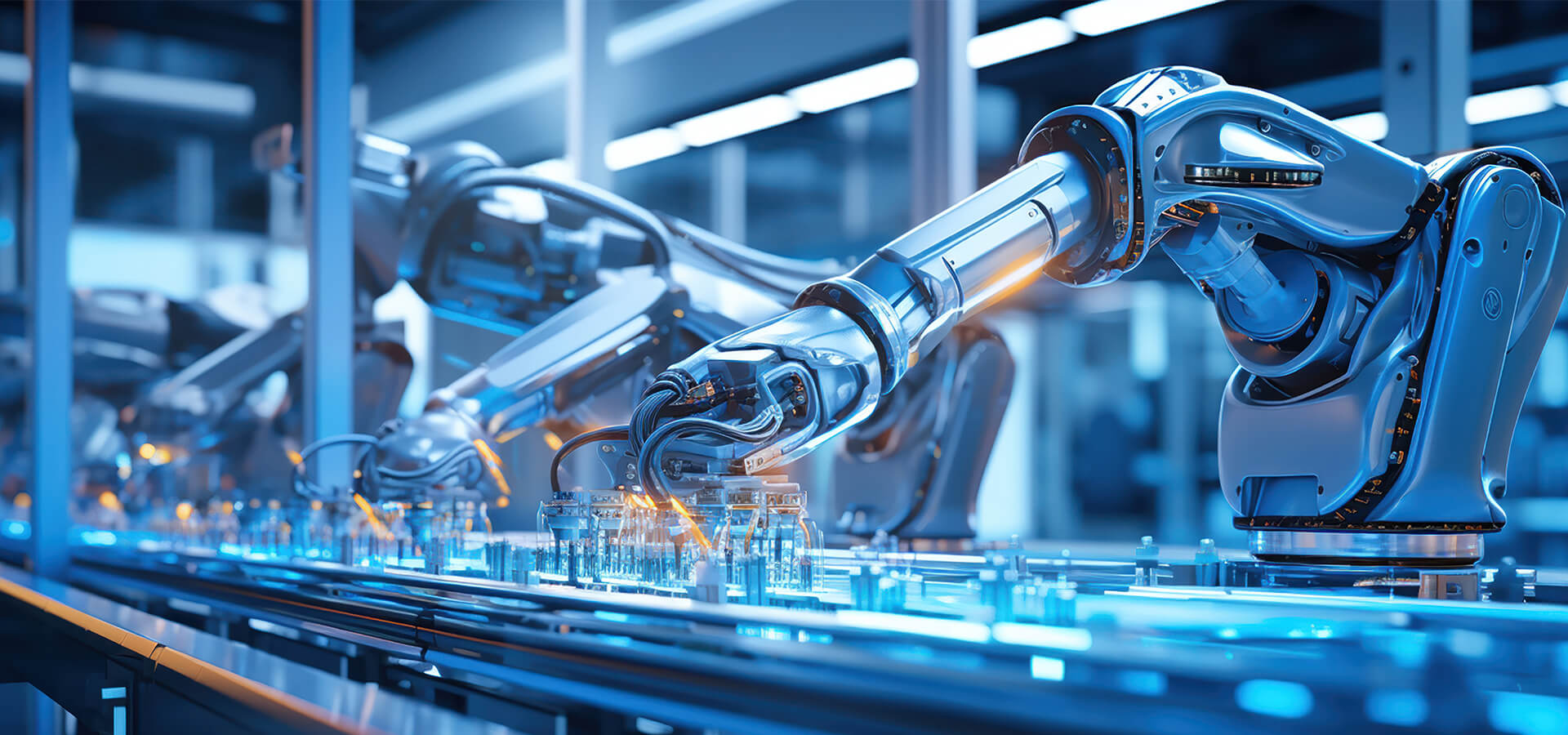
Stwórz Cyfrowego Bliźniaka Twojej fabryki!
Twórz zaawansowane symulacje 3D, analizuj dane i optymalizuj procesy w czasie rzeczywistym.
Dzięki technologii Digital Twin stworzysz wirtualną kopię swojego zakładu, która pozwoli na analizę, optymalizację i testowanie scenariuszy bez ingerencji w rzeczywistą produkcję.
Przewiduj awarie, testuj różne scenariusze „co jeśli?” i podejmuj najlepsze decyzje dzięki technologii Digital Twin!
Dowiedz się więcej
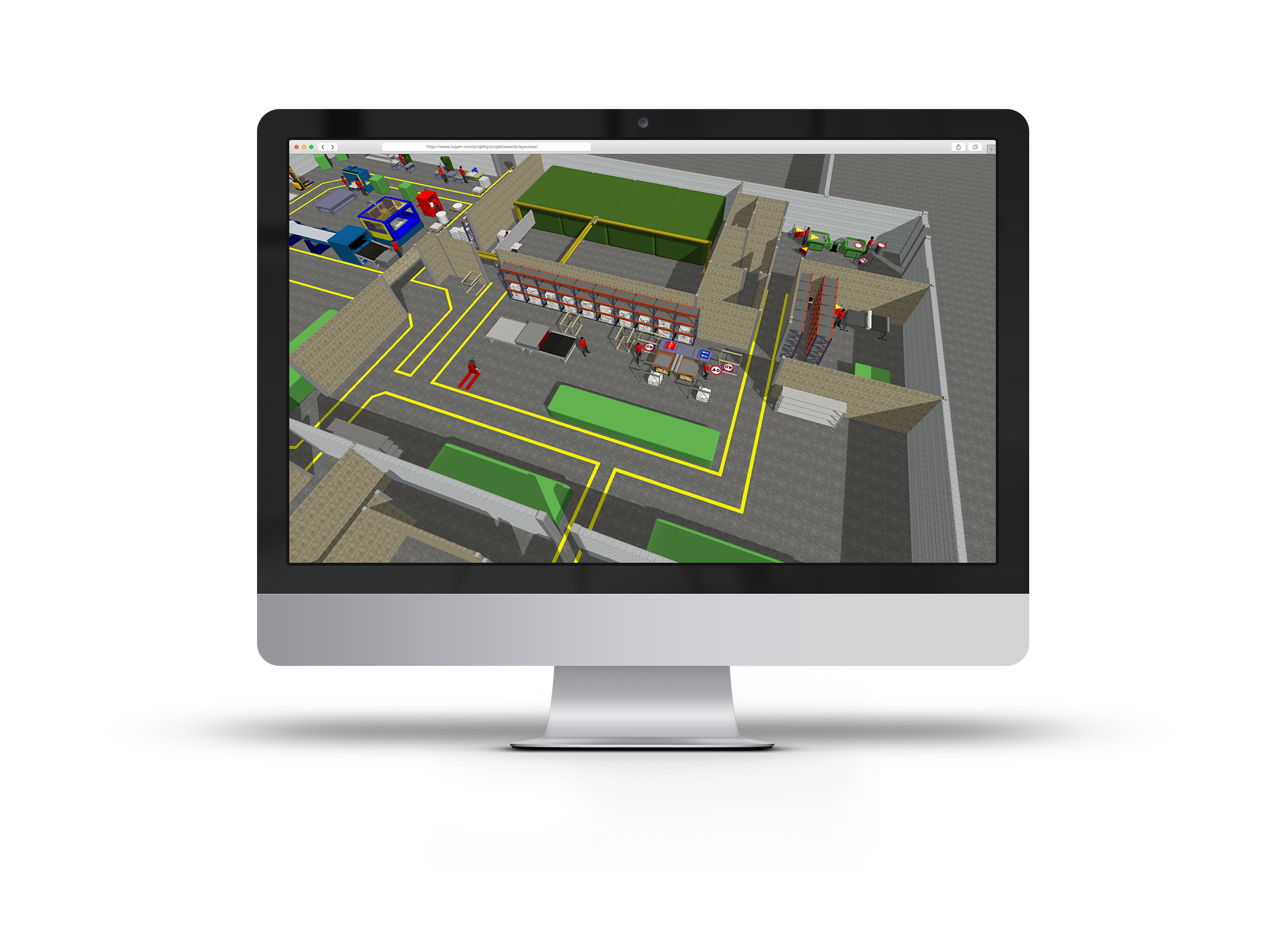
Digital Twin – nowoczesna technologia na wyciągnięcie ręki
Rozwiązania Industry 4.0
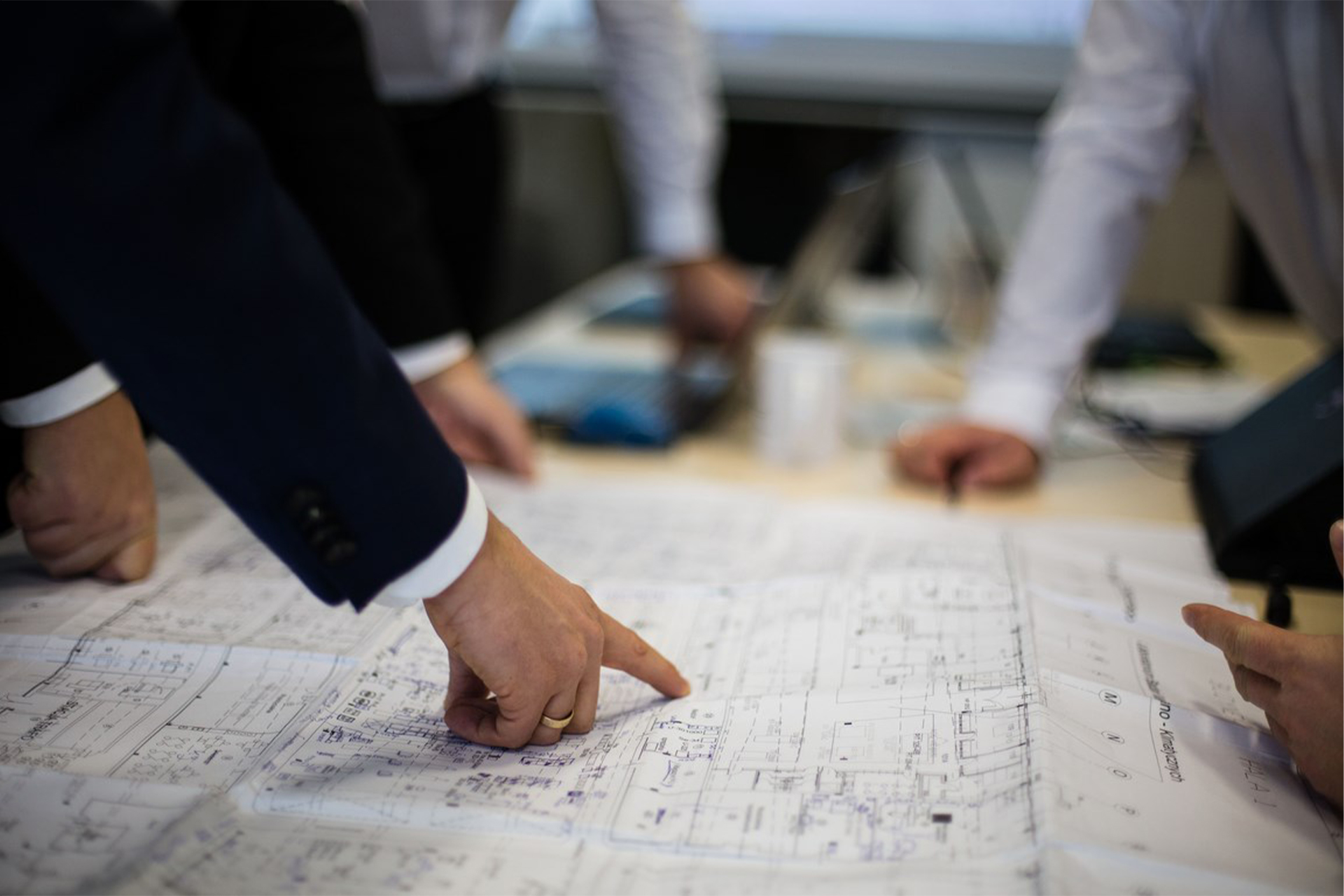
Projektowanie Layoutów 3D
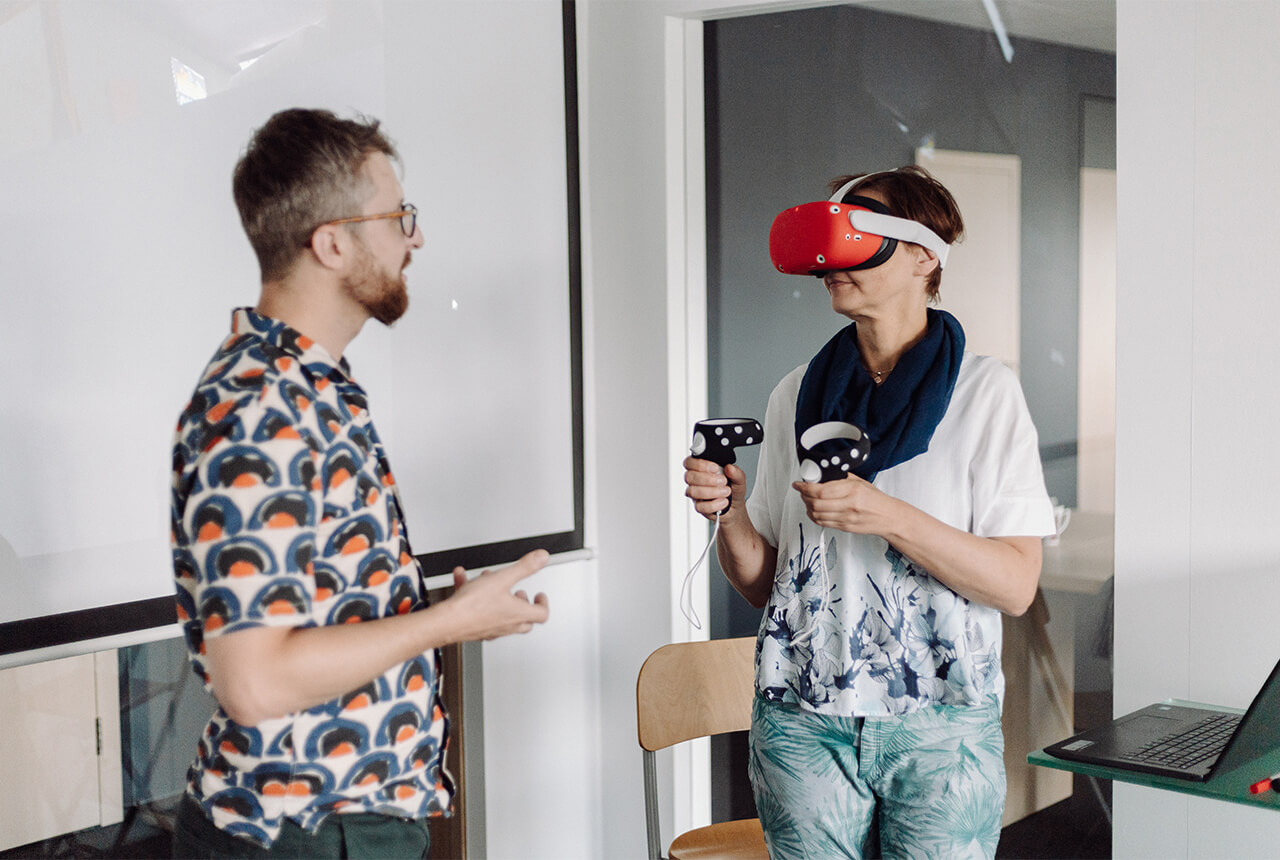
Wirtualna rzeczywistość VR
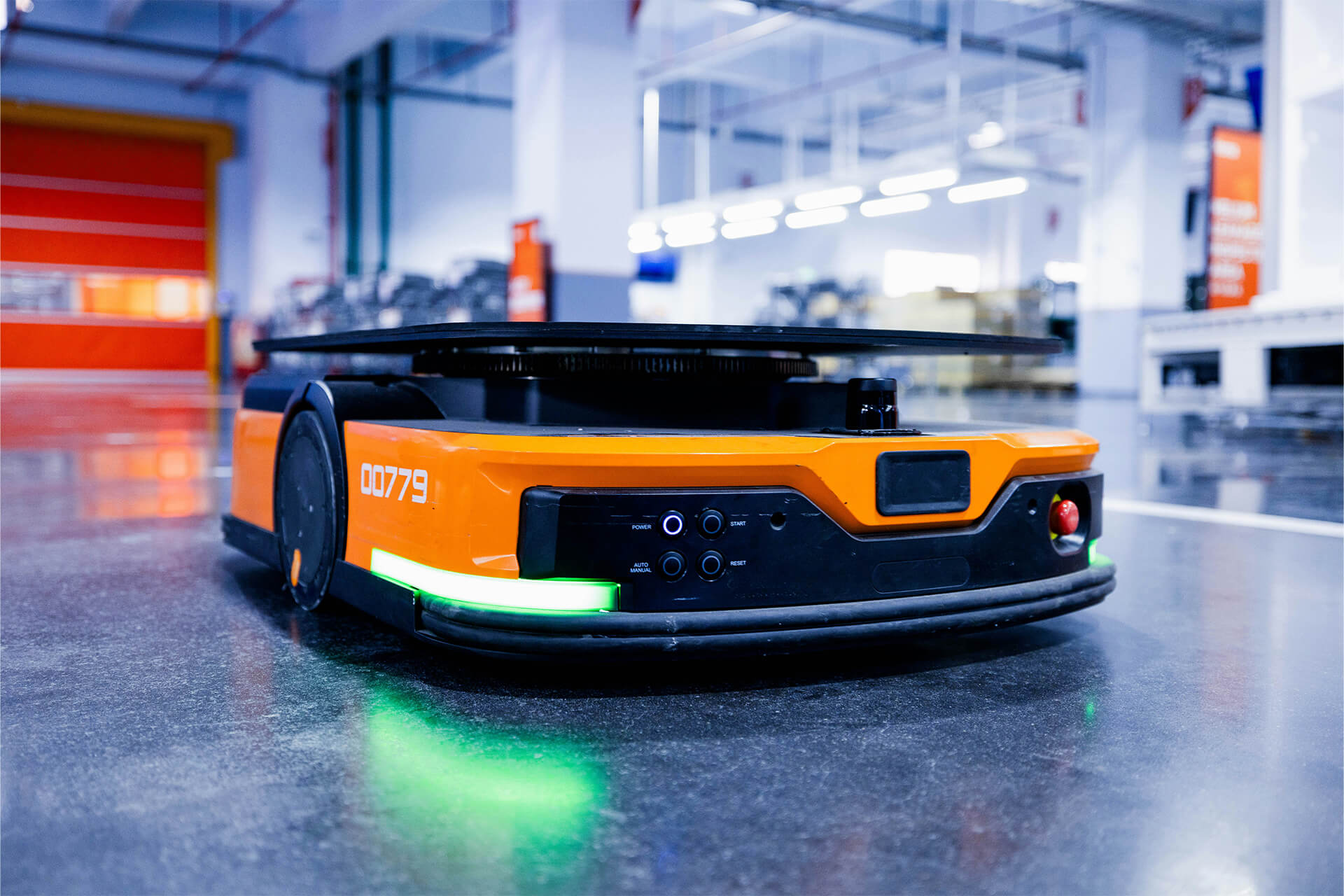
Wykorzystanie pojazdów autonomicznych AGV
Ile czasu zajmuje stworzenie Digital Twin?
Stworzenie Digital Twin zależy od kilku czynników, takich jak skala projektu, rodzaj modelowanego systemu, ilość danych i wymagane technologie.
Proste wdrożenia mogą zająć kilka dni lub tygodni, natomiast Cyfrowe Bliźniaki całych zakładów wymagają dużej liczby danych, przez co czas modelowania się zwiększa i może wynieść od kilku do kilkunastu miesięcy.
Iteracyjne wdrażanie, pozwala rozłożyć koszty i dostosować inwestycję do bieżących potrzeb.
Korzyści z wykorzystania Digital Twin
Kompleksowe wdrożenie lub przemyślana budowa krok po kroku
Proces tworzenia Digital Twin można realizować iteracyjnie, stopniowo rozwijając cyfrowego bliźniaka w zależności od potrzeb i dostępnych zasobów.
Czym jest Digital Twin?
Digital Twin to wirtualna kopia fizycznego systemu, obiektu lub procesu.
Jest to cyfrowy model dynamicznie reagujący na zmiany w swoim fizycznym odpowiedniku, pozwalający na przewidywanie jego przyszłych stanów i optymalizację, bez ingerencji w rzeczywistym świecie.
Ponadto wspiera zarządzanie produkcją w ramach rewolucji przemysłowej 4.0 jako zaawansowane narzędzie do symulacji komputerowej.
Umożliwia modelowanie złożonych systemów produkcyjnych i usługowych w 3D, a także symulacja wielu scenariuszy, co pozwala na optymalizację procesów.
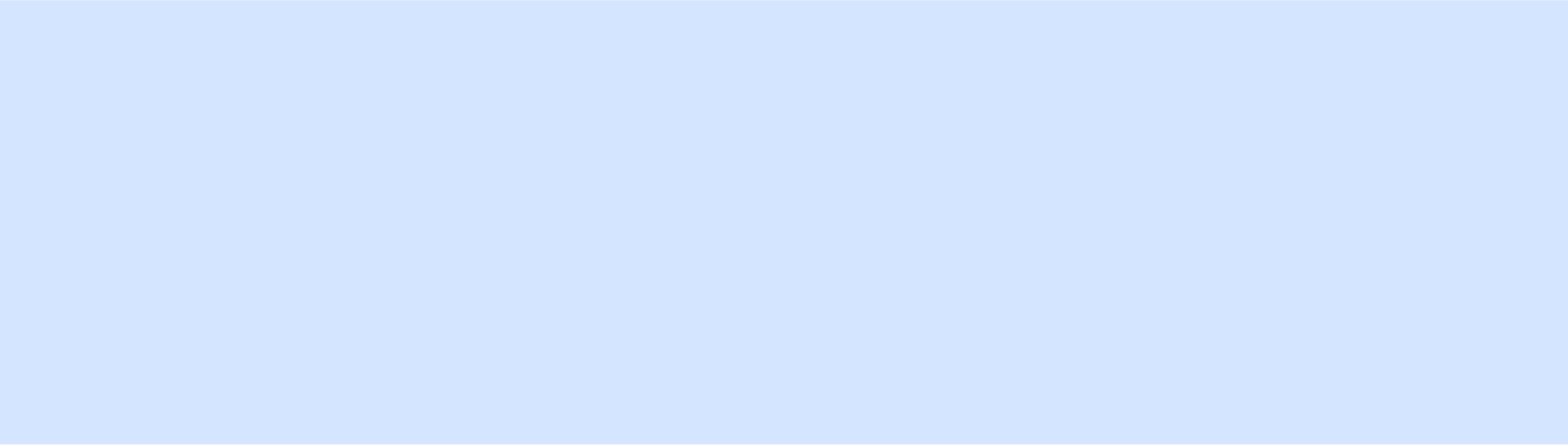
INDUSTRY 4.0 W POLSCE - RAPORT
Badanie stopnia implementacji rozwiązań z zakresu Industry 4.0
Zapraszamy do zapoznania się z wynikami najnowszego ogólnopolskiego badania dotyczącego poziomu wdrażania rozwiązań z zakresu Industry 4.0 w przedsiębiorstwach. Nasze badanie obejmowało różnorodne sektory przemysłu oraz rozmiary firm, aby dostarczyć kompleksowego obrazu stanu obecnego i trendów w zakresie cyfrowej transformacji.

Wypełnij formularz i pobierz raport!
Posłuchaj co o rewolucji Industry 4.0 mówią Eksperci LUQAM
Odcinek 1: Kartka i ołówek, tablet, a może Cyfrowy Bliźniak – dlaczego warto i jak modelować procesy? – cz. 1
Czy w dobie technologii warto trzymać się modelowania procesów za pomocą kartki i ołówka? Czy tablet jest lepszym wyborem? A może już najwyższa pora na wykorzystanie Digital Twin?
PODCAST

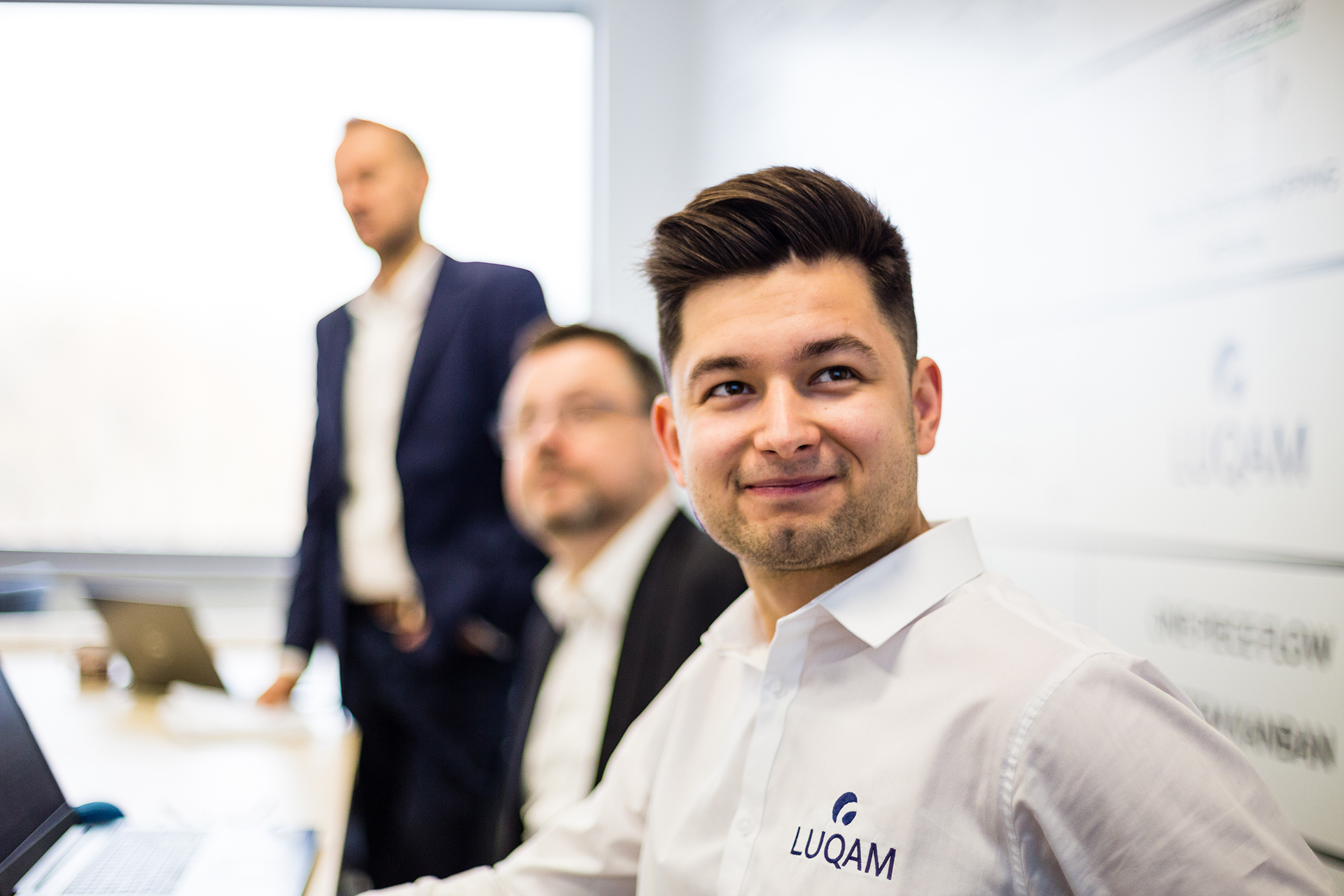
formularz kontaktowy
Porozmawiajmy o Digital Twin dla Twojej firmy!
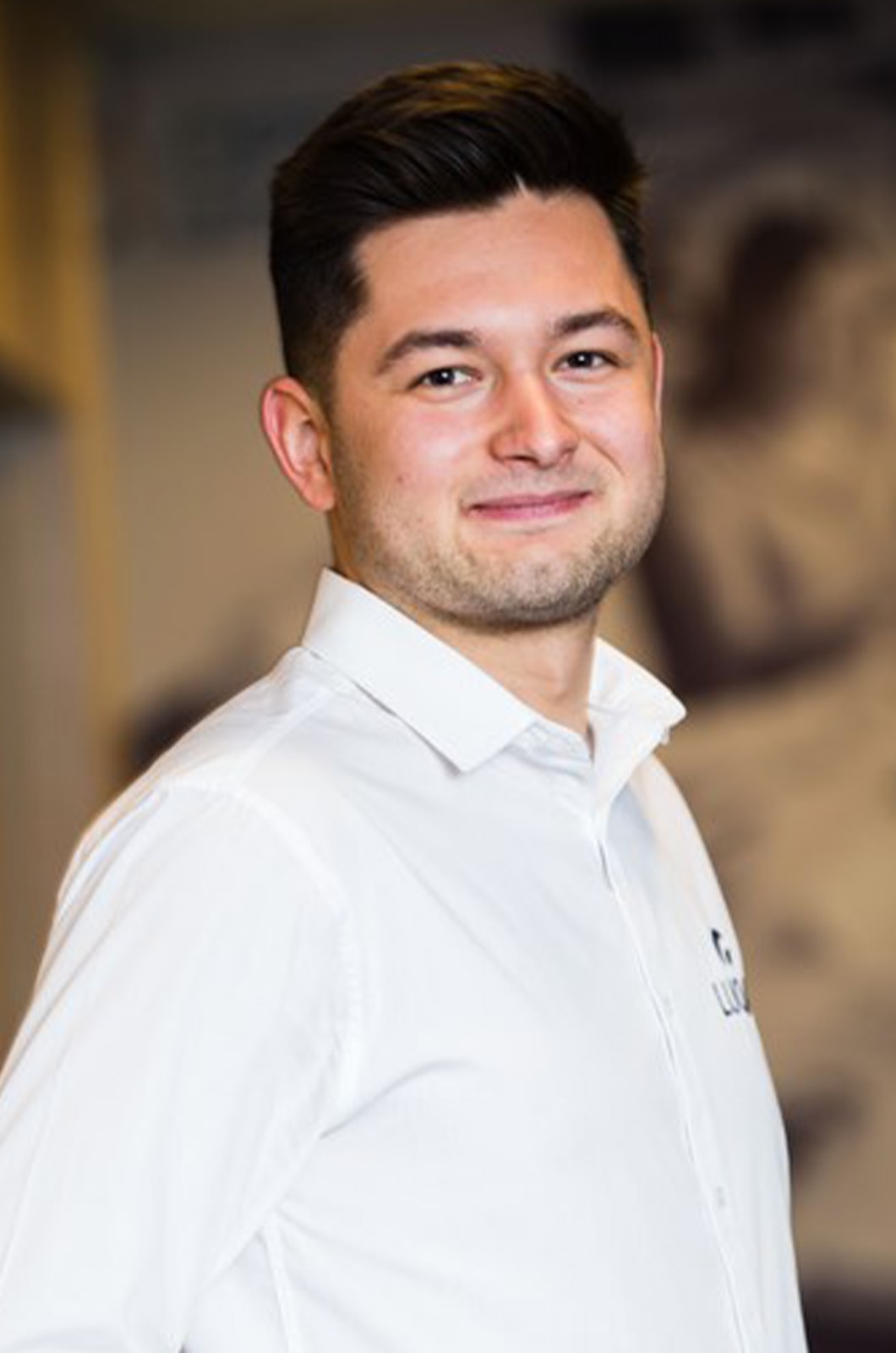
Arkadiusz Wzorek
newsletter